Технология на топене
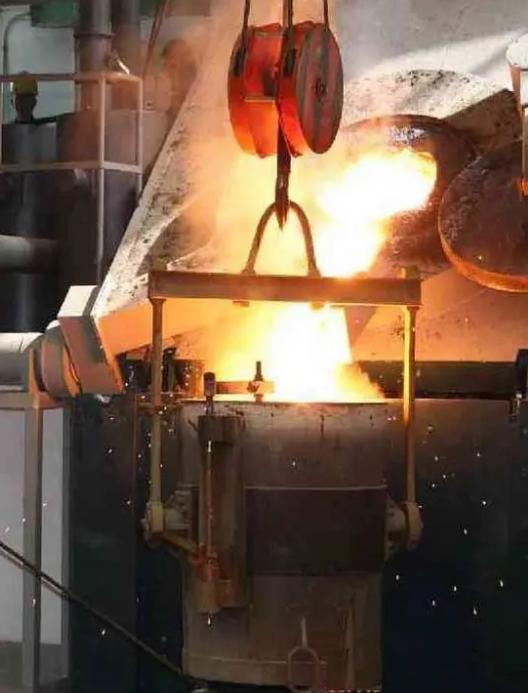
Понастоящем топенето на продукти за преработка на мед обикновено използва индукционна топилна пещ, а също така приема топене в реверберационна пещ и топене в шахтова пещ.
Топенето в индукционна пещ е подходящо за всички видове мед и медни сплави и има характеристиките на чисто топене и осигуряване на качеството на стопилката.Според структурата на пещта индукционните пещи се разделят на индукционни пещи със сърцевина и индукционни пещи без сърцевина.Индукционната пещ със сърцевина има характеристиките на висока производствена ефективност и висока термична ефективност и е подходяща за непрекъснато топене на едно разнообразие от мед и медни сплави, като червена мед и месинг.Индукционната пещ без ядро има характеристиките на бърза скорост на нагряване и лесна замяна на разновидности на сплави.Подходящ е за топене на мед и медни сплави с висока точка на топене и различни разновидности, като бронз и мелхиор.
Вакуумната индукционна пещ е индукционна пещ, оборудвана с вакуумна система, подходяща за топене на мед и медни сплави, които са лесни за вдишване и окисляване, като безкислородна мед, берилиев бронз, циркониев бронз, магнезиев бронз и др. за електрически вакуум.
Топенето в реверберационна пещ може да рафинира и премахне примесите от стопилката и се използва главно при топенето на скрап от мед.Шахтовата пещ е вид пещ за бързо непрекъснато топене, която има предимствата на висока топлинна ефективност, висока скорост на топене и удобно изключване на пещта.Може да се контролира;няма процес на рафиниране, така че по-голямата част от суровините трябва да бъдат катодна мед.Шахтовите пещи обикновено се използват с машини за непрекъснато леене за непрекъснато леене и могат да се използват и със задържащи пещи за полунепрекъснато леене.
Тенденцията на развитие на производствената технология за топене на мед се отразява главно в намаляване на загубата на суровини при изгаряне, намаляване на окисляването и вдишването на стопилката, подобряване на качеството на стопилката и приемане на висока ефективност (скоростта на топене на индукционната пещ е по-голяма от 10 t/h), широкомащабни (капацитетът на индукционната пещ може да бъде по-голям от 35 t/set), дълъг живот (животът на облицовката е 1 до 2 години) и енергоспестяващ (консумацията на енергия от индукционната пещта е по-малка от 360 kWh/t), пещта за задържане е оборудвана с дегазиращо устройство (дегазиране на CO газ), а индукционната пещ Сензорът приема структура на спрей, електрическото контролно оборудване приема двупосочен тиристор плюс захранване за преобразуване на честота, предварително нагряване на пещта, наблюдение на състоянието на пещта и температурното поле на огнеупора и алармена система, пещта за задържане е оборудвана с устройство за претегляне и контролът на температурата е по-точен.
Производствено оборудване - линия за разрязване
Производството на линия за рязане на медни ленти е производствена линия за непрекъснато рязане и рязане, която разширява широката намотка чрез размотавача, нарязва намотката на необходимата ширина чрез машината за нарязване и я пренавива на няколко намотки през навиващото устройство. (Стелаж за съхранение) Използвайте кран, за да съхранявате ролките върху стелажа за съхранение
↓
(Зареждане на кола) Използвайте захранващата количка, за да поставите ръчно ролката с материал върху барабана за размотаване и да я затегнете
↓
(Развиващ механизъм и притискаща ролка против разхлабване) Развийте намотката с помощта на водача за отваряне и притискащата ролка
↓
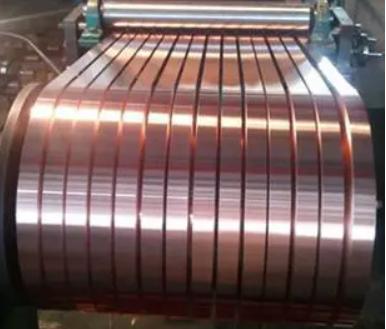
(NO·1 looper и люлеещ се мост) съхранение и буфер
↓
(Устройство за водач на ръба и прищипваща ролка) Вертикалните ролки водят листа в притискащите ролки, за да се предотврати отклонение, ширината и позиционирането на вертикалната направляваща ролка са регулируеми
↓
(Машина за рязане) влезте в машината за рязане за позициониране и рязане
↓
(Бързо сменяема въртяща се седалка) Смяна на група инструменти
↓
(Устройство за навиване на скрап) Нарежете скрап
↓(Направляваща маса в края на изхода и запушалка на опашката на намотката) Въведете бримка NO.2
↓
(люлеещ се мост и бримка NO.2) съхранение на материала и премахване на разликата в дебелината
↓
(Устройство за разделяне на напрежението на пресовата плоча и разширителния вал за въздух) осигурява сила на опън, разделяне на плочата и колана
↓
(Ножица за рязане, устройство за измерване на дължината на кормилното управление и водеща маса) измерване на дължината, сегментиране на намотка с фиксирана дължина, водач за резба на лента
↓
(навиващо устройство, устройство за разделяне, устройство за бутаща плоча) разделителна лента, навиване
↓
(разтоварен камион, опаковки) медна лента разтоварване и опаковане
Технология на горещо валцуване
Горещото валцуване се използва главно за валцоване на блокове за производство на листове, ленти и фолио.
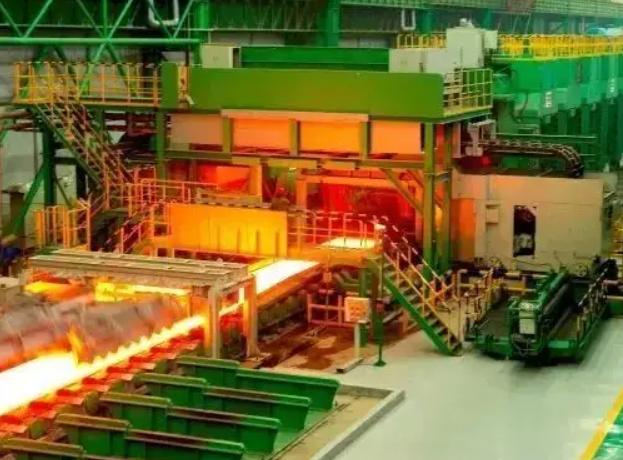
Спецификациите на блоковете за валцуване на заготовки трябва да вземат предвид фактори като разнообразие на продукта, производствен мащаб, метод на леене и т.н. и са свързани с условията на оборудването за валцуване (като отвор на ролката, диаметър на ролката, допустимо налягане при валцоване, мощност на двигателя и дължина на ролковата маса) и т.н.Обикновено съотношението между дебелината на слитъка и диаметъра на ролката е 1: (3,5~7): ширината обикновено е равна на или няколко пъти по-голяма от ширината на готовия продукт, а ширината и количеството на изрязване трябва да бъдат правилно разглеждан.Обикновено ширината на плочата трябва да бъде 80% от дължината на тялото на ролката.Дължината на блока трябва да бъде разумно обмислена в съответствие с производствените условия.Най-общо казано, при предпоставката, че крайната температура на валцуване при горещо валцуване може да се контролира, колкото по-дълъг е слитъкът, толкова по-висока е производствената ефективност и добивът.
Спецификациите на слитъка на малките и средни предприятия за преработка на мед обикновено са (60 ~ 150) mm × (220 ~ 450) mm × (2000 ~ 3200) mm, а теглото на слитъка е 1,5 ~ 3 t;спецификациите на слитъка на големите заводи за преработка на мед Обикновено е (150~250) mm × (630~1250) mm × (2400~8000) mm, а теглото на слитъка е 4,5~20 t.
По време на горещо валцуване температурата на повърхността на ролката се повишава рязко в момента, когато ролката е в контакт с високотемпературния валцуван детайл.Многократното термично разширение и студеното свиване причиняват пукнатини и пукнатини по повърхността на ролката.Следователно охлаждането и смазването трябва да се извършват по време на горещо валцуване.Обикновено вода или емулсия с по-ниска концентрация се използва като охлаждаща и смазваща среда.Общата работна скорост на горещо валцуване обикновено е 90% до 95%.Дебелината на горещо валцуваната лента обикновено е от 9 до 16 mm.Повърхностното фрезоване на лента след горещо валцуване може да отстрани повърхностните оксидни слоеве, навлизането на мащаб и други повърхностни дефекти, получени по време на леене, нагряване и горещо валцуване.В зависимост от тежестта на повърхностните дефекти на горещо валцуваната лента и нуждите на процеса, количеството на смилане на всяка страна е 0,25 до 0,5 mm.
Становете за горещо валцуване обикновено са реверсивни валцови мелници с две или четири височини.С увеличаването на слитъка и непрекъснатото удължаване на дължината на лентата, нивото на контрол и функцията на мелницата за горещо валцуване имат тенденция на непрекъснато подобрение и подобрение, като например използването на автоматичен контрол на дебелината, хидравлични огъващи ролки, предни и задни вертикални ролки, само охлаждащи ролки без охлаждане Устройство за валцоване, TP ролка (Taper Pis-ton Roll) контрол на короната, онлайн охлаждане (закаляване) след валцуване, онлайн навиване и други технологии за подобряване на еднаквостта на структурата и свойствата на лентата и получаване на по-добри плоча.
Технология на леене
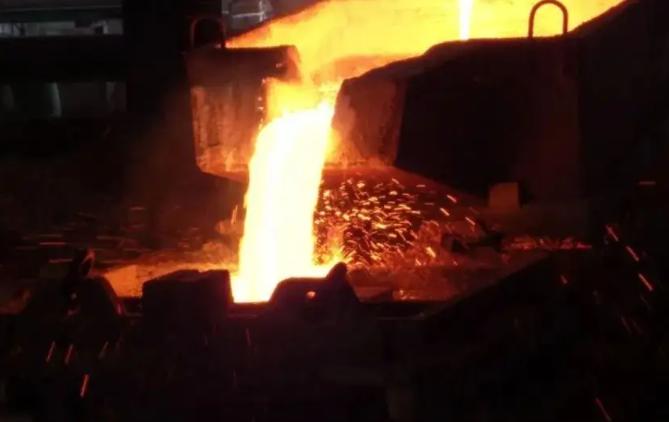
Леенето на мед и медни сплави обикновено се разделя на: вертикално полунепрекъснато леене, вертикално пълно непрекъснато леене, хоризонтално непрекъснато леене, непрекъснато леене нагоре и други технологии за леене.
A. Вертикално полунепрекъснато леене
Вертикалното полунепрекъснато леене има характеристиките на просто оборудване и гъвкаво производство и е подходящо за леене на различни кръгли и плоски слитъци от мед и медни сплави.Режимът на предаване на вертикална машина за полунепрекъснато леене е разделен на хидравличен, водещ винт и стоманено въже.Тъй като хидравличната трансмисия е относително стабилна, тя се използва повече.Кристализаторът може да вибрира с различни амплитуди и честоти според нуждите.Понастоящем методът на полунепрекъснато леене се използва широко при производството на слитъци от мед и медни сплави.
Б. Вертикално пълно непрекъснато леене
Вертикалното пълно непрекъснато леене има характеристиките на голяма производителност и висок добив (около 98%), подходящо за широкомащабно и непрекъснато производство на блокове с един сорт и спецификация и се превръща в един от основните методи за избор за топене и леене процес на модерни широкомащабни производствени линии за медни ленти.Вертикалната пълна непрекъсната леярска форма приема безконтактно лазерно автоматично управление на нивото на течността.Машината за леене обикновено използва хидравлично затягане, механична трансмисия, онлайн охлаждано с масло сухо рязане и събиране на стружки, автоматично маркиране и накланяне на блока.Структурата е сложна и степента на автоматизация е висока.
В. Хоризонтално непрекъснато леене
Хоризонталното непрекъснато леене може да произвежда заготовки и телени заготовки.
Хоризонталното непрекъснато леене на ленти може да произвежда ленти от мед и медни сплави с дебелина 14-20 mm.Лентите в този диапазон на дебелина могат да бъдат директно студено валцувани без горещо валцуване, така че те често се използват за производство на сплави, които са трудни за горещо валцуване (като калай, фосфорен бронз, оловен месинг и др.), могат също да произвеждат месинг, мелхиор и лента от ниско легирана медна сплав.В зависимост от ширината на леярската лента, хоризонталното непрекъснато леене може да лее от 1 до 4 ленти едновременно.Често използваните хоризонтални машини за непрекъснато леене могат да леят две ленти едновременно, всяка с ширина по-малка от 450 mm, или да леят една лента с ширина на лентата 650-900 mm.Хоризонталната лента за непрекъснато леене обикновено приема процеса на леене на издърпване-стоп-обратно натискане и има периодични линии на кристализация на повърхността, които обикновено трябва да бъдат елиминирани чрез смилане.Има местни примери за медни ленти с висока повърхност, които могат да бъдат произведени чрез изтегляне и леене на лентови заготовки без фрезоване.
Хоризонталното непрекъснато леене на заготовки за тръби, пръти и тел може да лее от 1 до 20 блока едновременно според различни сплави и спецификации.Обикновено диаметърът на заготовката на пръта или телта е от 6 до 400 mm, а външният диаметър на заготовката на тръбата е от 25 до 300 mm.Дебелината на стената е 5-50 mm, а дължината на страната на блока е 20-300 mm.Предимствата на метода на хоризонтално непрекъснато леене са, че процесът е кратък, производствените разходи са ниски и ефективността на производството е висока.В същото време това е и необходим производствен метод за някои сплави с лоша обработваемост на горещо.Напоследък това е основният метод за изработване на заготовки от често използвани медни продукти като калаено-фосфорни бронзови ленти, ленти от цинк-никелова сплав и медни тръби за климатизация, дезоксидирани с фосфор.производствени методи.
Недостатъците на метода за производство на хоризонтално непрекъснато леене са: подходящите сортове сплави са сравнително прости, консумацията на графитен материал във вътрешната втулка на матрицата е сравнително голяма и еднородността на кристалната структура на напречното сечение на блока не е лесен за управление.Долната част на слитъка се охлажда непрекъснато поради ефекта на гравитацията, който е близо до вътрешната стена на формата, а зърната са по-фини;горната част се дължи на образуването на въздушни междини и високата температура на стопилка, което причинява забавяне на втвърдяването на слитъка, което забавя скоростта на охлаждане и прави хистерезис на втвърдяването на слитъка.Кристалната структура е сравнително груба, което е особено очевидно за блокове с големи размери.С оглед на горните недостатъци в момента се разработва методът за леене с вертикално огъване със заготовка.Немска компания използва непрекъснато леярско устройство за вертикално огъване, за да тества отливането на (16-18) mm × 680 mm ламаринени бронзови ленти като DHP и CuSn6 при скорост от 600 mm/min.
D. Непрекъснато леене нагоре
Непрекъснатото леене нагоре е технология за леене, която се разви бързо през последните 20 до 30 години и се използва широко в производството на телени заготовки за ярки медни пръти.Той използва принципа на леене с вакуумно засмукване и възприема технологията stop-pull за реализиране на непрекъснато леене с няколко глави.Той има характеристиките на просто оборудване, малка инвестиция, по-малко загуба на метал и процедури за ниско замърсяване на околната среда.Непрекъснатото леене нагоре обикновено е подходящо за производство на заготовки от червена мед и безкислородна медна тел.Новото постижение през последните години е популяризирането и приложението му в тръбни заготовки с голям диаметър, месинг и мелхиор.Понастоящем е разработен възходящ агрегат за непрекъснато леене с годишна производителност от 5000 t и диаметър над Φ100 mm;бинарни обикновени месингови и цинково-бяли медни трикомпонентни сплави са били произведени и добивът на телените заготовки може да достигне повече от 90%.
E. Други техники за леене
Технологията за непрекъснато леене на заготовки е в процес на разработка.Той преодолява дефектите като петна, образувани по външната повърхност на заготовката поради процеса на спиране и изтегляне на непрекъснатото леене нагоре, а качеството на повърхността е отлично.И поради неговите почти насочени характеристики на втвърдяване, вътрешната структура е по-равномерна и чиста, така че производителността на продукта също е по-добра.Технологията на производство на заготовки от медна тел за непрекъснато леене на лента е широко използвана в големи производствени линии над 3 тона.Площта на напречното сечение на плочата обикновено е повече от 2000 mm2 и е последвана от непрекъсната валцова мелница с висока производствена ефективност.
Електромагнитното леене е изпробвано в моята страна още през 70-те години на миналия век, но промишленото производство не е реализирано.През последните години технологията за електромагнитно леене отбеляза голям напредък.Понастоящем безкислородни медни слитъци от Φ200 mm са успешно отлети с гладка повърхност.В същото време ефектът на разбъркване на електромагнитното поле върху стопилката може да насърчи отстраняването на отработените газове и шлаката и може да се получи безкислородна мед със съдържание на кислород по-малко от 0,001%.
Посоката на новата технология за леене на медни сплави е да се подобри структурата на матрицата чрез насочено втвърдяване, бързо втвърдяване, полутвърдо формоване, електромагнитно разбъркване, метаморфна обработка, автоматичен контрол на нивото на течността и други технически средства според теорията на втвърдяването., уплътняване, пречистване и реализиране на непрекъсната работа и формоване в близкия край.
В дългосрочен план леенето на мед и медни сплави ще бъде съжителството на технология за полунепрекъснато леене и технология за пълно непрекъснато леене, а делът на приложението на технологията за непрекъснато леене ще продължи да се увеличава.
Технология за студено валцуване
Съгласно спецификацията на валцуваната лента и процеса на валцуване, студеното валцуване се подразделя на валцуване, междинно валцуване и окончателно валцуване.Процесът на студено валцуване на отлятата лента с дебелина от 14 до 16 mm и горещо валцуваната заготовка с дебелина от около 5 до 16 mm до 2 до 6 mm се нарича разтягане, а процесът на продължаващо намаляване на дебелината на валцованото парче се нарича междинно валцуване., окончателното студено валцуване, за да отговори на изискванията на готовия продукт, се нарича окончателно валцуване.
Процесът на студено валцуване трябва да контролира системата за редуциране (обща скорост на обработка, скорост на обработка на преминаване и скорост на обработка на готовия продукт) в съответствие с различни сплави, спецификации на валцоване и изисквания за производителност на готовия продукт, разумен избор и регулиране на формата на ролката и разумен избор на смазване метод и лубрикант.Измерване и регулиране на напрежението.
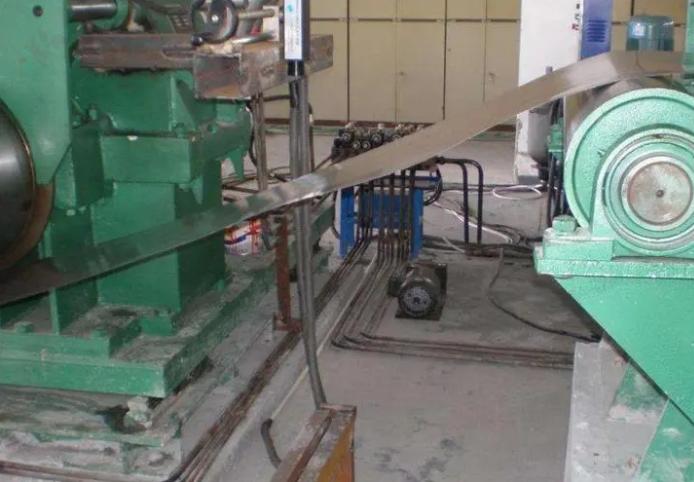
Мелниците за студено валцоване обикновено използват реверсивни валцови мелници с четири или няколко височини.Съвременните мелници за студено валцуване обикновено използват серия от технологии като хидравлично положително и отрицателно огъване на валци, автоматичен контрол на дебелината, налягането и напрежението, аксиално движение на ролките, сегментно охлаждане на ролките, автоматично управление на формата на плочата и автоматично подравняване на валцуваните детайли , за да може да се подобри точността на лентата.До 0,25±0,005 mm и в рамките на 5I от формата на пластината.
Тенденцията на развитие на технологията за студено валцуване се отразява в разработването и прилагането на високопрецизни многовалцови мелници, по-високи скорости на валцоване, по-точен контрол на дебелината и формата на лентата и спомагателни технологии като охлаждане, смазване, навиване, центриране и бързо валцуване промяна.усъвършенстване и др.
Производствено оборудване-Звънцова пещ
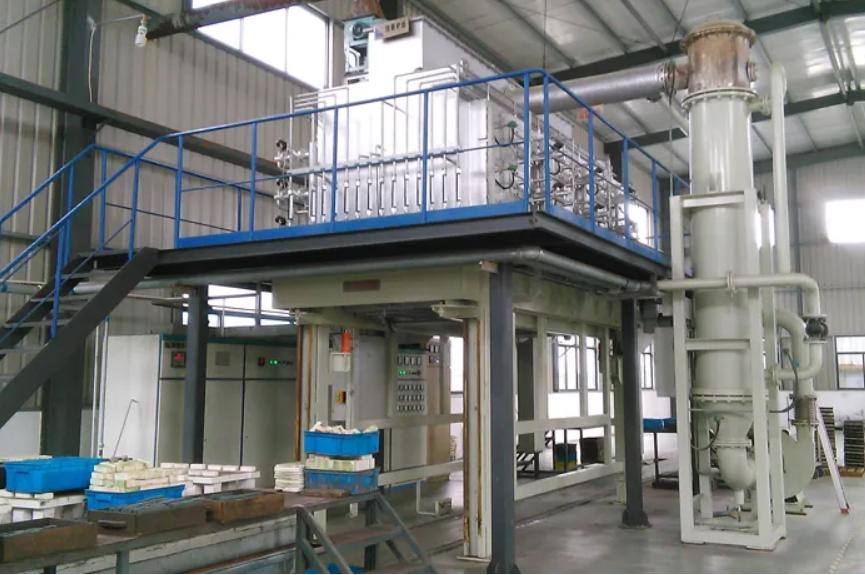
Камбановите пещи и подемните пещи обикновено се използват в промишлено производство и пилотни тестове.Като цяло мощността е голяма и консумацията на енергия е голяма.За промишлени предприятия материалът на пещта на повдигащата пещ Luoyang Sigma е керамично влакно, което има добър енергоспестяващ ефект, ниска консумация на енергия и ниска консумация на енергия.Спестете електроенергия и време, което е от полза за увеличаване на производството.
Преди двадесет и пет години германските BRANDS и Philips, водеща компания в индустрията за производство на ферит, съвместно разработиха нова машина за синтероване.Разработването на това оборудване отговаря на специалните нужди на феритната индустрия.По време на този процес BRANDS Bell Furnace непрекъснато се актуализира.
Той обръща внимание на нуждите на световноизвестни компании като Philips, Siemens, TDK, FDK и др., които също се възползват много от висококачественото оборудване на BRANDS.
Благодарение на високата стабилност на продуктите, произведени от камбанови пещи, камбановите пещи се превърнаха в водещите компании в професионалната индустрия за производство на ферит.Преди двадесет и пет години първата пещ, произведена от BRANDS, все още произвежда висококачествени продукти за Philips.
Основната характеристика на пещта за синтероване, предлагана от камбановата пещ, е нейната висока ефективност.Неговата интелигентна система за управление и друго оборудване образуват цялостна функционална единица, която може напълно да отговори на почти най-съвременните изисквания на феритната индустрия.
Клиентите на камбанкови пещи могат да програмират и съхраняват всеки температурен/атмосферен профил, необходим за производството на висококачествени продукти.Освен това клиентите могат да произвеждат всякакви други продукти навреме според действителните нужди, като по този начин съкращават времето за изпълнение и намаляват разходите.Оборудването за синтероване трябва да има добра регулируемост, за да произвежда разнообразие от различни продукти, за да се адаптира непрекъснато към нуждите на пазара.Това означава, че съответните продукти трябва да бъдат произведени според нуждите на отделния клиент.
Един добър производител на ферити може да произведе повече от 1000 различни магнита, за да отговори на специалните нужди на клиентите.Те изискват способността за повторение на процеса на синтероване с висока точност.Системите за камбанкови пещи се превърнаха в стандартни пещи за всички производители на ферити.
Във феритната индустрия тези пещи се използват главно за ниска консумация на енергия и ферити с висока μ стойност, особено в комуникационната индустрия.Невъзможно е да се произвеждат висококачествени сърцевини без камбанна пещ.
Камбаничната пещ изисква само няколко оператора по време на синтероването, товаренето и разтоварването могат да бъдат завършени през деня, а синтероването може да бъде завършено през нощта, което позволява пиково бръснене на електроенергия, което е много практично в днешната ситуация на недостиг на електроенергия.Камбанковите пещи произвеждат висококачествени продукти и всички допълнителни инвестиции бързо се възстановяват благодарение на висококачествените продукти.Контролът на температурата и атмосферата, дизайнът на пещта и контролът на въздушния поток в пещта са идеално интегрирани, за да осигурят равномерно нагряване и охлаждане на продукта.Контролът на атмосферата на пещта по време на охлаждане е пряко свързан с температурата на пещта и може да гарантира съдържание на кислород от 0,005% или дори по-ниско.И това са неща, които нашите конкуренти не могат да направят.
Благодарение на пълната система за въвеждане на буквено-цифрово програмиране, дългите процеси на синтероване могат лесно да бъдат възпроизведени, като по този начин се гарантира качеството на продукта.Когато продавате продукт, това е и отражение на качеството на продукта.
Технология на топлинна обработка
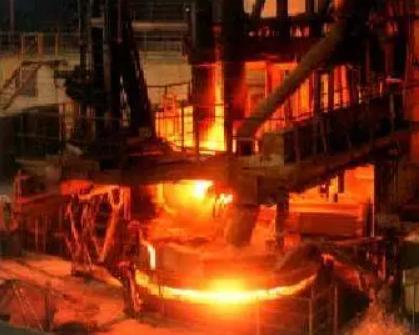
Няколко блокчета сплав (ленти) със силно отделяне на дендрити или напрежение при леене, като калай-фосфорен бронз, трябва да преминат през специално хомогенизиращо отгряване, което обикновено се извършва в камбанова пещ.Температурата на хомогенизиращо отгряване обикновено е между 600 и 750°C.
Понастоящем по-голямата част от междинното отгряване (рекристализиращо отгряване) и завършеното отгряване (отгряване за контролиране на състоянието и производителността на продукта) на ленти от медна сплав са ярко отгрявани чрез газова защита.Типовете пещи включват камбанова пещ, пещ с въздушна възглавница, вертикална тягова пещ и др. Окислителното отгряване постепенно се премахва.
Тенденцията на развитие на технологията за топлинна обработка се отразява в горещо валцуваната онлайн обработка на разтвор на утаено-укрепени легирани материали и последващата технология за термична обработка на деформация, непрекъснато светло отгряване и отгряване на напрежение в защитна атмосфера.
Закаляване — Термичната обработка със стареене се използва главно за подлежащо на термична обработка укрепване на медни сплави.Чрез топлинна обработка продуктът променя своята микроструктура и придобива необходимите специални свойства.С развитието на сплави с висока якост и висока проводимост, процесът на термична обработка със закаляване и стареене ще бъде по-приложен.Оборудването за обработка на стареене е приблизително същото като оборудването за отгряване.
Екструзионна технология
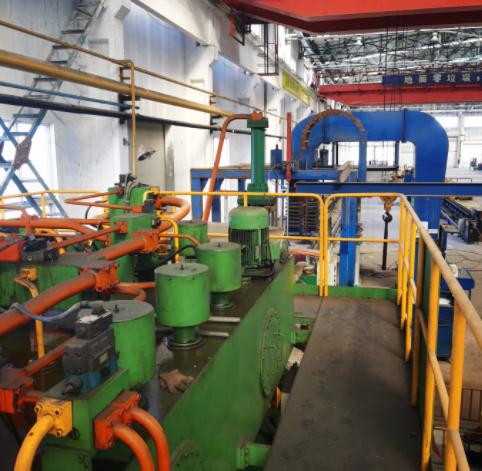
Екструзията е зрял и усъвършенстван метод за производство на тръби, пръти, профили и доставка на медни тръби и медни сплави.Чрез смяна на матрицата или използване на метода на екструдиране с перфорация, различни разновидности на сплави и различни форми на напречното сечение могат да бъдат директно екструдирани.Чрез екструдиране отлятата структура на слитъка се променя в обработена структура, а екструдираната тръбна заготовка и заготовката на пръчките имат висока точност на размерите и структурата е фина и равномерна.Методът на екструдиране е производствен метод, който обикновено се използва от местни и чуждестранни производители на медни тръби и пръти.
Коването на медни сплави се извършва главно от производители на машини в моята страна, включително свободно коване и щанцоване, като големи зъбни колела, червячни зъбни колела, червячни зъбни колела за автомобилни синхронизатори и др.
Методът на екструзия може да бъде разделен на три вида: екструзия напред, обратна екструзия и специална екструзия.Сред тях има много приложения на екструдиране напред, обратно екструдиране се използва при производството на малки и средни пръчки и телове, а специално екструдиране се използва в специално производство.
При екструдиране, според свойствата на сплавта, техническите изисквания на екструдираните продукти и капацитета и структурата на екструдера, типът, размерът и коефициентът на екструдиране на блока трябва да бъдат разумно избрани, така че степента на деформация да е не по-малко от 85%.Температурата на екструдиране и скоростта на екструдиране са основните параметри на процеса на екструдиране и разумният температурен диапазон на екструдиране трябва да се определи според диаграмата на пластичност и фазовата диаграма на метала.За медта и медните сплави температурата на екструзия обикновено е между 570 и 950 °C, а температурата на екструзия от мед е дори от 1000 до 1050 °C.В сравнение с температурата на нагряване на екструзионния цилиндър от 400 до 450 °C, температурната разлика между двете е относително висока.Ако скоростта на екструзия е твърде ниска, температурата на повърхността на слитъка ще спадне твърде бързо, което ще доведе до увеличаване на неравномерността на потока на метала, което ще доведе до увеличаване на натоварването при екструзия и дори ще причини скучен феномен .Следователно медта и медните сплави обикновено използват сравнително високоскоростна екструзия, скоростта на екструзия може да достигне повече от 50 mm/s.
Когато се екструдират мед и медни сплави, често се използва екструдиране на пилинг за отстраняване на повърхностни дефекти на слитъка, а дебелината на пилинг е 1-2 m.Водното запечатване обикновено се използва на изхода на екструзионната заготовка, така че продуктът да може да се охлади в резервоара за вода след екструдиране и повърхността на продукта да не се окислява и последващата студена обработка може да се извърши без ецване.Той има тенденция да използва екструдер с голям тонаж със синхронно поемащо устройство за екструдиране на тръбни или телени рулони с единично тегло над 500 kg, така че ефективно да подобри производствената ефективност и цялостния добив на последващата последователност.Понастоящем производството на тръби от мед и медни сплави използва най-вече хоризонтални хидравлични екструдери напред с независима перфорационна система (двойно действие) и директно предаване на маслена помпа, а производството на пръти най-вече приема не-независима перфорационна система (едно действие) и маслена помпа директно предаване.Хоризонтален хидравличен екструдер напред или назад.Обикновено използваните спецификации на екструдера са 8-50 MN, а сега има тенденция да се произвежда от екструдери с голям тонаж над 40 MN, за да се увеличи единичното тегло на блока, като по този начин се подобри ефективността на производството и добива.
Съвременните хоризонтални хидравлични екструдери са структурно оборудвани с предварително напрегната интегрална рамка, водач и опора за екструзионен цилиндър "X", вградена система за перфорация, вътрешно охлаждане на перфорационната игла, плъзгаща се или ротационна матрица и устройство за бърза смяна на матрицата, високомощна променлива маслена помпа директно задвижване, интегриран логически клапан, PLC контрол и други модерни технологии, оборудването има висока точност, компактна структура, стабилна работа, безопасно блокиране и лесен за реализиране програмен контрол.Технологията за непрекъснато екструдиране (Conform) постигна известен напредък през последните десет години, особено за производството на пръти със специална форма, като проводници за електрически локомотиви, което е много обещаващо.През последните десетилетия новата технология за екструдиране се разви бързо и тенденцията на развитие на технологията за екструдиране се въплъщава, както следва: (1) Оборудване за екструдиране.Силата на екструдиране на пресата за екструдиране ще се развие в по-голяма посока и пресата за екструдиране с повече от 30MN ще се превърне в основно тяло, а автоматизацията на производствената линия за преса за екструдиране ще продължи да се подобрява.Съвременните машини за екструдиране са напълно възприели компютърно програмно управление и програмируемо логическо управление, така че ефективността на производството е значително подобрена, операторите са значително намалени и дори е възможно да се реализира автоматична безпилотна работа на екструзионни производствени линии.
Структурата на тялото на екструдера също непрекъснато се подобрява и усъвършенства.През последните години някои хоризонтални екструдери са приели предварително напрегната рамка, за да гарантират стабилността на цялостната структура.Съвременният екструдер реализира методите на предна и обратна екструзия.Екструдерът е оборудван с два екструзионни вала (основен екструзионен вал и вал на матрицата).По време на екструзия екструзионният цилиндър се движи заедно с главния вал.Понастоящем продуктът е. Посоката на изтичане е в съответствие с посоката на движение на главния вал и противоположна на относителната посока на движение на оста на матрицата.Основата на матрицата на екструдера също приема конфигурация от множество станции, което не само улеснява смяната на матрицата, но също така подобрява ефективността на производството.Съвременните екструдери използват лазерно устройство за контрол на настройката на отклонението, което предоставя ефективни данни за състоянието на централната линия на екструдиране, което е удобно за навременна и бърза настройка.Хидравличната преса с директно задвижване на помпата за високо налягане, използваща масло като работна среда, напълно замени хидравличната преса.Инструментите за екструдиране също се актуализират постоянно с развитието на технологията за екструдиране.Иглата за пробиване с вътрешно водно охлаждане е широко популяризирана, а иглата за пробиване и търкаляне с променливо напречно сечение значително подобрява ефекта на смазване.По-широко използвани са керамичните форми и формите от легирана стомана с по-дълъг живот и по-високо качество на повърхността.
Инструментите за екструдиране също се актуализират постоянно с развитието на технологията за екструдиране.Иглата за пробиване с вътрешно водно охлаждане е широко популяризирана, а иглата за пробиване и търкаляне с променливо напречно сечение значително подобрява ефекта на смазване.Приложението на керамични форми и форми от легирана стомана с по-дълъг живот и по-високо качество на повърхността е по-популярно.(2) Екструзионен производствен процес.Разновидностите и спецификациите на екструдираните продукти непрекъснато се разширяват.Екструзията на малки сечения, ултра-високо прецизни тръби, пръти, профили и супер-големи профили гарантира качеството на външния вид на продуктите, намалява вътрешните дефекти на продуктите, намалява геометричните загуби и допълнително насърчава методите на екструдиране като еднакво представяне на екструдирания продукти.Широко приложение намира и съвременната технология за обратно екструдиране.За лесно окисляващи се метали се използва екструдиране с водно уплътнение, което може да намали замърсяването от ецване, да намали загубата на метал и да подобри качеството на повърхността на продуктите.За екструдирани продукти, които трябва да бъдат закалени, просто контролирайте подходящата температура.Методът на екструдиране с водно уплътнение може да постигне целта, ефективно да съкрати производствения цикъл и да спести енергия.
С непрекъснатото подобряване на капацитета на екструдера и технологията за екструдиране постепенно се прилага модерна технология за екструдиране, като изотермична екструзия, екструзия с охлаждаща матрица, високоскоростна екструзия и други технологии за екструдиране напред, обратна екструзия, хидростатична екструзия Практическото приложение на технологията за непрекъсната екструзия на пресоване и съответствие, прилагането на екструзия на прах и технология за екструдиране на слоести композити на нискотемпературни свръхпроводящи материали, разработването на нови методи като екструдиране на полутвърд метал и екструдиране на множество заготовки, разработването на малки прецизни части, технология за формоване чрез студена екструзия, и т.н., са бързо разработени и широко разработени и приложени.
Спектрометър
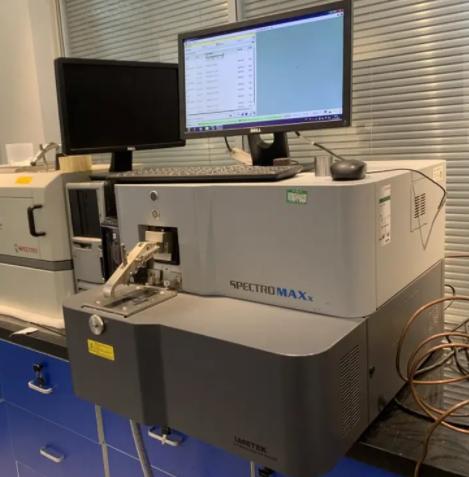
Спектроскопът е научен инструмент, който разлага светлина със сложен състав на спектрални линии.Седемцветната светлина в слънчевата светлина е частта, която невъоръженото око може да различи (видима светлина), но ако слънчевата светлина се разложи от спектрометър и се подреди според дължината на вълната, видимата светлина заема само малък диапазон в спектъра, а останалите са спектри, които не могат да бъдат разграничени с просто око, като инфрачервени лъчи, микровълни, UV лъчи, рентгенови лъчи и др. Оптичната информация се улавя от спектрометъра, проявява се с фотографски филм или се показва и анализира от компютъризиран автоматичен дисплей цифров инструмент, за да открие какви елементи се съдържат в изделието.Тази технология се използва широко при откриване на замърсяване на въздуха, замърсяване на водата, хигиена на храните, металургия и др.
Спектрометърът, известен също като спектрометър, е широко известен като спектрометър с директно отчитане.Устройство, което измерва интензитета на спектралните линии при различни дължини на вълната с фотодетектори като фотоумножителни тръби.Състои се от входящ процеп, дисперсионна система, система за изображения и един или повече изходни процепи.Електромагнитното излъчване на източника на радиация се разделя на необходимата дължина на вълната или област от дължина на вълната чрез диспергиращия елемент и интензитетът се измерва при избраната дължина на вълната (или сканиране на определена лента).Има два вида монохроматори и полихроматори.
Изпитващ инструмент-кондуктометър
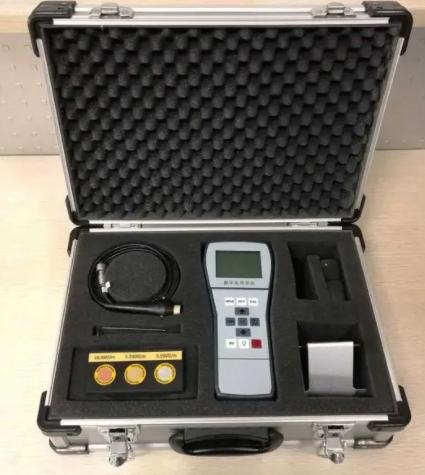
Цифровият ръчен метален тестер за проводимост (кондуктометър) FD-101 прилага принципа на откриване на вихрови токове и е специално проектиран според изискванията за проводимост на електрическата индустрия.Той отговаря на стандартите за изпитване на металната индустрия по отношение на функция и точност.
1. Кондуктометърът FD-101 има три уникални:
1) Единственият китайски кондуктомер, който е преминал проверката на Института по аеронавигационни материали;
2) Единственият китайски измервател на проводимост, който може да отговори на нуждите на компаниите в самолетната индустрия;
3) Единственият китайски кондуктометър, изнасян в много страни.
2. Представяне на функцията на продукта:
1) Голям диапазон на измерване: 6,9%IACS-110%IACS(4,0MS/m-64MS/m), който отговаря на теста за проводимост на всички цветни метали.
2) Интелигентно калибриране: бързо и точно, напълно избягване на грешки при ръчно калибриране.
3) Инструментът има добра температурна компенсация: показанията автоматично се компенсират до стойността при 20 °C и корекцията не се влияе от човешка грешка.
4) Добра стабилност: това е вашата лична охрана за контрол на качеството.
5) Хуманизиран интелигентен софтуер: Той ви предоставя удобен интерфейс за откриване и мощни функции за обработка и събиране на данни.
6) Удобна работа: производственият обект и лабораторията могат да се използват навсякъде, спечелвайки благоволението на мнозинството потребители.
7) Самостоятелна подмяна на сонди: Всеки хост може да бъде оборудван с множество сонди и потребителите могат да ги сменят по всяко време.
8) Числова резолюция: 0,1% IACS (MS/m)
9) Интерфейсът за измерване едновременно показва стойностите на измерването в две единици %IACS и MS/m.
10) Има функцията да съхранява данни от измерванията.
Тестер за твърдост
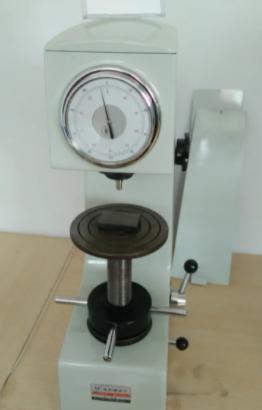
Инструментът приема уникален и прецизен дизайн по отношение на механиката, оптиката и източника на светлина, което прави изображението на вдлъбнатината по-ясно и измерването по-точно.И двата обектива 20x и 40x могат да участват в измерването, което прави обхвата на измерване по-голям и приложението по-обширно.Инструментът е оборудван с цифров измервателен микроскоп, който може да показва метода на изпитване, силата на изпитване, дължината на вдлъбнатината, стойността на твърдостта, времето за задържане на силата на изпитване, времената на измерване и т.н. на течния екран и има интерфейс с резба, който може да бъде свързан към цифров фотоапарат и CCD камера.Има известна представителност в домашните продукти за глава.
Инструмент за тестване - детектор за съпротивление
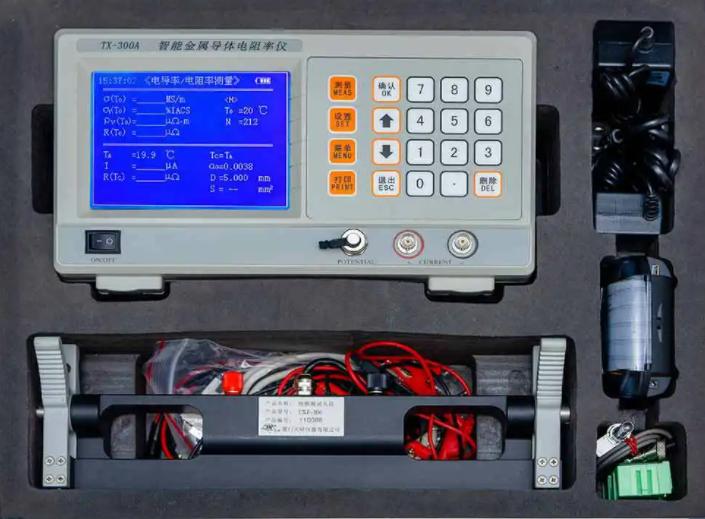
Инструментът за измерване на съпротивление на метална тел е високоефективен инструмент за изпитване на параметри като съпротивление на тел, пръти и електрическа проводимост.Неговата производителност напълно отговаря на съответните технически изисквания в GB/T3048.2 и GB/T3048.4.Широко използван в металургията, електричеството, проводниците и кабелите, електрическите уреди, колежите и университетите, научноизследователските звена и други индустрии.
Основни характеристики на инструмента:
(1) Той интегрира усъвършенствана електронна технология, технология с един чип и технология за автоматично откриване, със силна функция за автоматизация и проста работа;
(2) Просто натиснете бутона веднъж, всички измерени стойности могат да бъдат получени без никакви изчисления, подходящи за непрекъснато, бързо и точно откриване;
(3) Дизайн, захранван от батерии, малък размер, лесен за носене, подходящ за използване на полето и полето;
(4) Голям екран, голям шрифт, може да показва съпротивление, проводимост, съпротивление и други измерени стойности и температура, тестов ток, коефициент на температурна компенсация и други спомагателни параметри едновременно, много интуитивно;
(5) Една машина е многофункционална, с 3 интерфейса за измерване, а именно интерфейс за измерване на съпротивление на проводник и проводимост, интерфейс за измерване на всеобхватни параметри на кабела и интерфейс за измерване на съпротивление на DC кабел (тип TX-300B);
(6) Всяко измерване има функциите за автоматичен избор на постоянен ток, автоматична комутация на тока, автоматична корекция на нулевата точка и автоматична корекция на температурната компенсация, за да се гарантира точността на всяка стойност на измерване;
(7) Уникалното преносимо приспособление за тестване с четири извода е подходящо за бързо измерване на различни материали и различни спецификации на проводници или пръти;
(8) Вградена памет за данни, която може да записва и запазва 1000 комплекта данни от измервания и измервателни параметри и да се свързва към горния компютър, за да генерира пълен отчет.